Bite splints are designed at the DSD Planning Center using Exocad 3D planning software
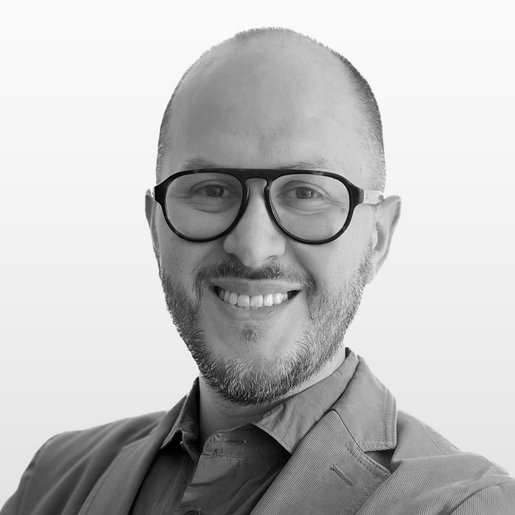
By Eduardo Peraza
⋅ 2 min read
⋅ 9 Oct 2023
What are the factors that contribute to a great quality 3D printed bite splint? We know that the material selection and splint design contribute to patient comfort, which leads to higher compliance, ensuring better patient outcomes.
In the Bite Splint Masterclass we collaborate with Formlabs Dental to address this question and bring dentists an in-depth view of digitally designing and printing bite splints. At the DSD Planning Center, we always recommend a bite splint as a standard product to include with every smile restoration, ensuring that patients can take great care of their new smiles.
I’m Eduardo Peraza, Quality Control Manager at the DSD Planning Center, and in this article I share some insights that the team and I apply to designing bite splints or occlusal guards for 3D printing.
3D Planning Software for Bite Splint Design
To begin with designing a Michigan bite splint, the STL files for each arch are reviewed before being imported into the Exocad 3D planning software. Once uploaded, the occlusion needs to be checked. Adding a transparency effect to the STL of the lower arch creates a detailed view of the occlusion from the lower angle.
Our goal is always:
to have adequate space and clearance for the bite splint
for the bite splint surface to be as flat as possible
to achieve centric contacts on all teeth, ensuring they touch simultaneously in centric occlusion
To have no gaps or intercuspations
The thickness of the bite splint is guided by the points above in addition to the virtual articulator measurements and 3D printer materials recommendations. For example, in the case of the Formlabs Dental LT Comfort Resin, the ideal minimum occlusal thickness is 2mm and the minimum lateral thickness is 1mm.
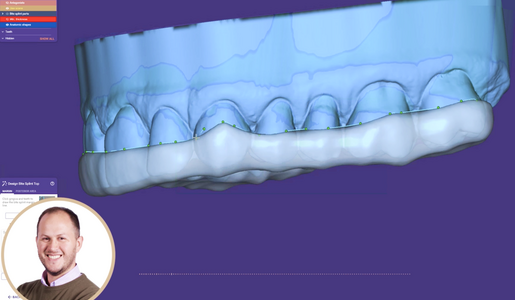
Accommodating excursive movements
It is essential for a bite splint to accommodate excursive movements, including the disocclusion, the protrusive movement with posterior disocclusion, the right movement with left disocclusion, and the left movement with right disocclusion. This is considered to be a classic design for the bite.
From here the lower model is brought forward to perform the protrusive movement. Pause here and examine it from the sides as follows:
Check the side where there is no contact at all
Examine the protrusive movement and ensure centric contacts with all teeth touching
Perform the protrusive movement with posterior disocclusion on the other side
Observe the centric relationship
Take a closer look from a lower perspective
Proceed all the way to the front, examining which teeth are making contact
Confirm that canine guidance is satisfactory from this perspective
Avoiding interference on the non-working side
The most important part at this stage of the design is to avoid interference on the non-working side. Initially, there might be some contact on the right as it moves to the left, but ensure there are no contacts on the non-working side.
Check for any remaining contact at the back
Confirm that the centric contacts design design are completely flat without any interdentation
Ensure that all teeth make contact and that exclusive moments are perfectly aligned with the protrusive
Activate canine guidance on both sides
Aim for a delicate splint with an occlusion thickness of around 1.5mm but approximately 1mm on the buccal side
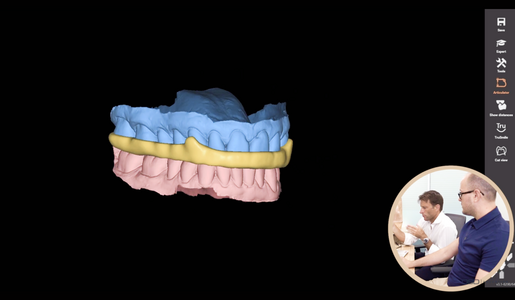
Christian Coachman and Eduardo Peraza designing a bite split using Exocad software
To avoid spots on the buccal side of the splint, following Formlabs Dental’s recommendations, measure the thinnest part of the buccal aspect. Confirm that the thickness is satisfactory and remove the model. After this step, the bite splint design is ready to be sent to the 3D printer and printed according to the material manufacturer’s recommendations.
Ready to start 3D printing bite splints?
DSD's partnership with Formlabs Dental demonstrates our commitment to advancing dental technology and innovative education to equip dental professionals with the knowledge and tools they need to truly excel in their offices and levels of patient care.
If you’re interested in more detailed information about the Formlabs Dental printers we trust at DSD, check out our full guide to all products we print on Formlabs Dental 3D printers.